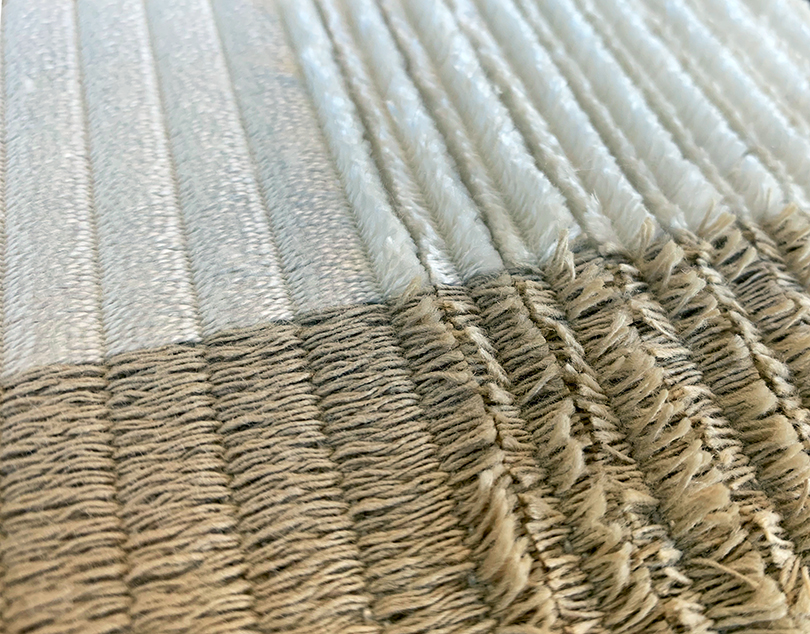
Corduroy has had a bit of a revival in recent years and it is a great fabric to play around with weaving. It’s a fairly simple structure which only requires four shafts.
Corduroy is a ribbed fabric with a velvet like-feel to it. It has warp-wise ridges which are cut to create a pile. Due to their structure corduroys tend to be a heavier fabric and used for clothes such as coats, trousers, suits as well as for interiors.
When manufactured the ridges (ribs) tend to be quite narrow. The ribs are called ‘wales’. For standard clothing the number of wales per inch is around 10-12 but can vary from 6 (jumbo cord) to 18 (needle or pin cord).
The ribs are made up of stripes of weft floats with a narrow plain weave between them which is there to secure the floats down. The ground cloth behind is what holds everything together. These floats are cut down the center to create the characteristic pile.
Below is the woven structure I used to weave my corduroy. I did make mine super chunky as you can see from the fabric pictures above. This was to allow me to easily see what was going on.
The corduroy below only uses four shafts. Two are for the plain weave background and the other two secure the floats down with plain weave. The picks alternate between one pick of weaving the plain weave background and two which weave the floats.
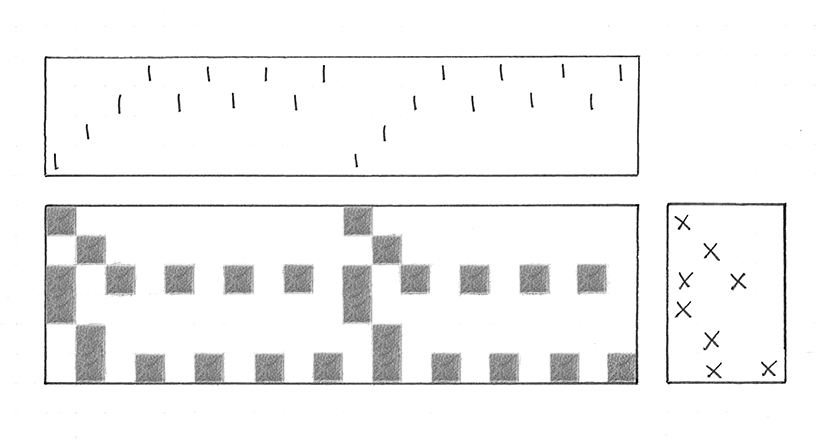
The corduroy in the image above was woven using 2/20nm spun silk and tussah silk. It was intested to see what effect the tussah silk had in comparison to the spun silk in terms of texture. The spun silk is so soft and luxurious while the tussah is more spikey. It would be fun to experiment how different yarns effect the texture of the pile.
When weaving I beat down quite firmly to ensure that the ground cloth was strong and the plain weave would hold the floats in place when cut. It is only the plain weave on shafts 1 and 2 that stop the floats from coming out.
To cut the floats I found it best to cut them while the fabric was still on the loom and under tension. I cut them as I went along, once I had woven about 5cm or so. The scissors need to be very sharp, small and pointy. The first couple of pairs of scissors I used were not small and sharp enough. Every time I cut the floats the scissors just pulled the weft floats out of the structure. It may take a few tries to find the right ones and of course as the width of the ribs gets smaller the scissors need to get smaller too.
A twill can also be used for the ground cloth. This will enable the cloth to be beaten down more and increase the density of the floats making a more luxurious fabric. Weaving the floats so that they are not all exactly the same width will also give a more rounded shape to the ribs.
A lot of fun fabrics could be created by varying the yarn type, width of rib and where the floats are cut (do they all need to be cut)?